Как в Ю. Корее устроено производство нижней ретортной пленки для формирования лотков для автоклавирования.
Друзья, привет!
Как мы обещали ранее, мы с вами делимся историями посещения других предприятий. В частности, мы посетили одно из крупных предприятий корпорации Донгвон. Это предприятие по выпуску барьерной ретортной термоформуемой нижней пленки. И, в частности, увидели отдельный участок, как из этой пленки формуются готовые лотки.
На предприятии размещено оборудование, одно из самых лучших в мире — оборудование немецкой корпорации ILLIG. И сейчас мы пройдемся и посмотрим, как производится эта барьерная пленка. Для того, чтобы произвести трехслойную барьерную пленку используется несколько экструдеров. Базовая основная пленка - полипропилен снаружи и изнутри, и межслойный барьерный слой EVOH, который также совмещается с полипропиленовой пленкой, и для этого используются слои адгезива.
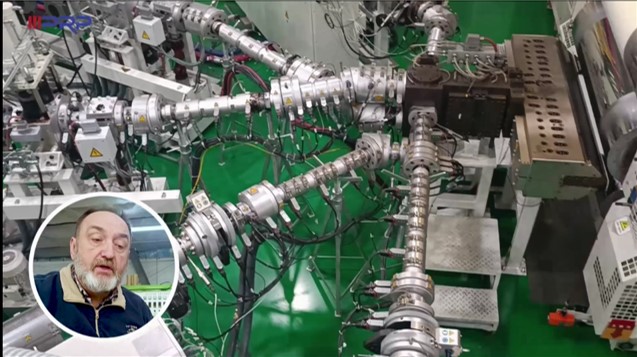
Вот сейчас сверху можно будет наблюдать отдельные подачи каждого компонента. И так называемый паук из пяти экструдеров подводит расплавленный материал непосредственно к голове. Голова щелевой экструзии, плоскощелевая экструзия.
А это разводка трубопроводов подачи гранулята, потому что емкость для хранения находится в другом помещении. Далее секция охлаждения экструдированного материала с отбором нагара, запаха, дыма: и дальнейшая вытяжка пленки, резка ее на форматы для того, чтобы можно было использовать в последующем производстве. Так на вакуум-формуемых машинах, так и на машинах для производства лотков.
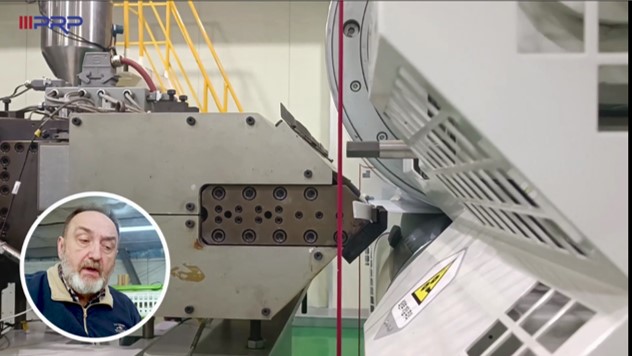
Машина непрерывного цикла выполнена таким образом, что можно в любой ее части посмотреть, насколько аккуратно все происходит. То есть машина с доступными местами, узлами, что очень удобно для пользователя. И мы видим, собственно, полотно. То есть, если вдруг появляется какой-то дефект, он достаточно быстро может быть определён и обнаружен.
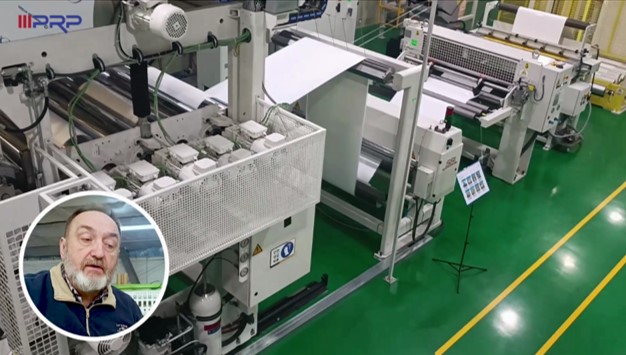
Далее после вытяжки из машины материал попадает на узел обрезки кромки, и уже четко сформированное полотно попадает в зону автоматической намотки. Рулоны получаются большие, безусловно, ручного труда здесь уже не может быть. И рулон в непрерывном цикле сменяется новым. Наматывается уже готовый рулон и удаляется в помещение для хранения. Отдельное помещение для хранения со строгим режимом температурного контроля, поэтому гарантия сохранности плёнки очень высокая.
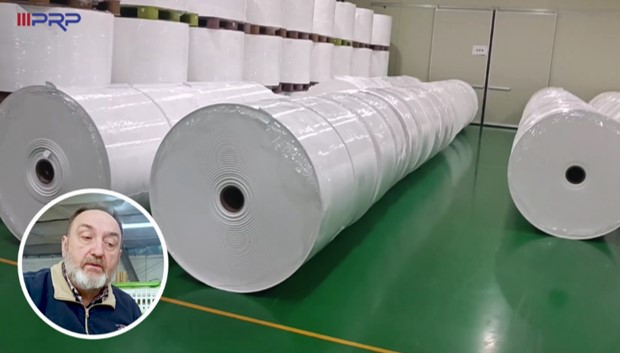
Следующее помещение, куда мы нам удалось попасть — это помещение по выпуску готовых форм. В частности, в Корее очень широкого распространа упаковка риса в ретортных лотках. Они уже очень широко представлены и в России. Полотно с рулона попадает в зону предварительного подогрева, потом попадает внутрь машины, где происходит формование изделия, и можно даже через прозрачные стенки видеть, как происходит вырубка и удаление готового изделия.
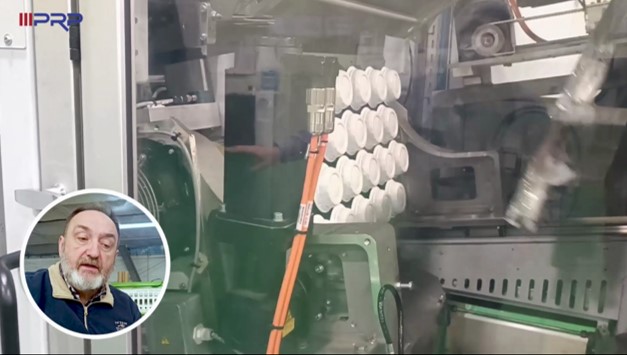
Автоматический робот принимает отформованные вырубленные лотки и отправляет их на узел стекинга, то есть сбора в пачки. Когда автоматически принимается решение, что формовка прошла некачественно, машина сама сбрасывает эти лотки, и они удаляются.
Внешне лоток может выглядеть очень здорово, но если в этой партии затесался хотя бы один нестандартный лоток, либо лоток с дефектом, то машина удаляет лотки всего цикла. То есть здесь предупреждается попадание брака во всю партию
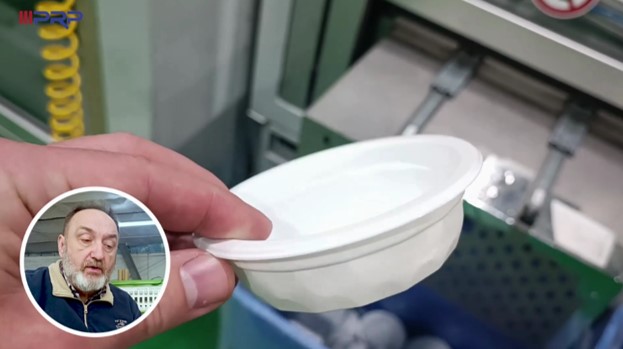
Далее уже сформованные лотки попадают на участок зрительной, визуальной, так сказать, проверки операторами. Облой удаляется в отдельную машину, где превращается в крошку.
Операторы стопками определенного количества по 20-25 штук отправляют лотки в контрольную машину, которая еще оптическими устройствами полностью контролирует качество каждого лотка. Эта стопка перебирается шаг за шагом, лоток за лотком, при помощи визуального, оптического контроля зон обрезки. Компьютер определяет на соответствие стандартам. Ну и, безусловно, машина потом формирует пачку требуемого количества, и оператор упаковывает ее в транспортную тару.
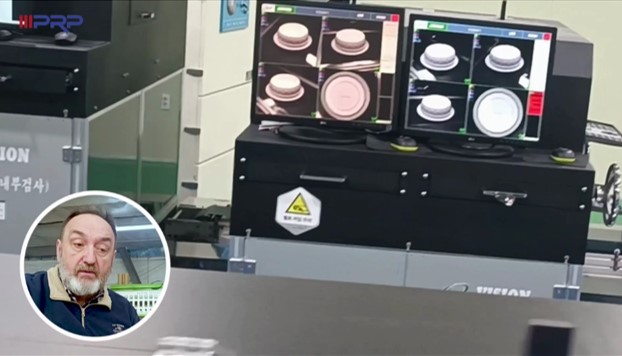
На всей линии задействовано всего 4 человека, которые работают с готовой продукцией, все остальные процессы полностью автоматизированы. Ну и в фирменных коробках производитель отправляет эти лотки дальше.
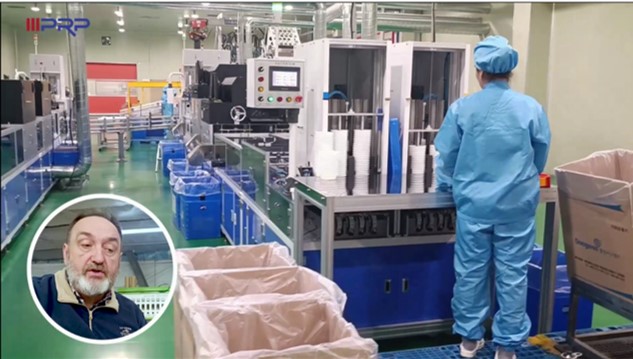
Когда мы попали на этот участок вместе с нашими партнерами, нам технари завода позволили даже "засунуть свой нос", свою голову во внутрь машины, чтобы разобраться в деталях с теми или иными процессами. Очень большой интерес вызывал процесс нагрева барьерной пленки, потому что полипропиленовая пленка специфична для формования, рассказали этапности барабанного нагрева, когда пленка проходит через несколько барабанов, равномерно прогревается, и в этом случае она становится как резиновая - для легкого формования.
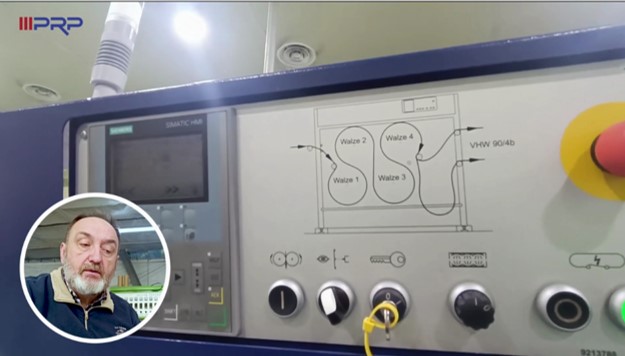
Технический директор предприятия объясняет, для чего нужен плавный прогрев всего полотна. Пленка очень толстая, прогрев идет сверху и снизу, с обеих сторон пленки. Пленка прогревается, устраняется идея неравномерного прогрева, и только потом пленка попадает в зону дополнительно нагрева инфракрасными нагревателями перед формованием.
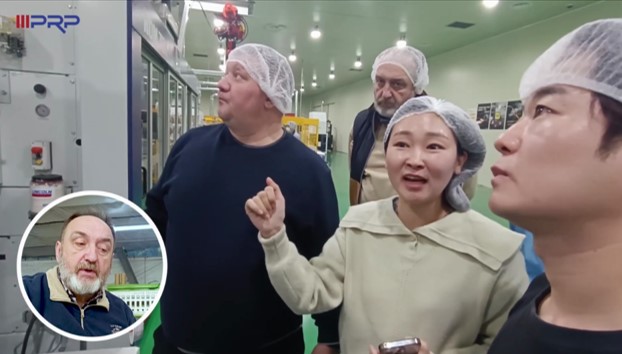
… Идет непосредственное уточнение, чтобы не оставалось вопросов, что удобно на предприятии, когда мы видим сразу и материал, и изделия, и технических специалистов, которые все вопросы сразу проясняют. Снова клиенту все уточняют, потому что на его оборудовании процесс нагрева может происходить совершенно другими методами, например зонными нагревами.
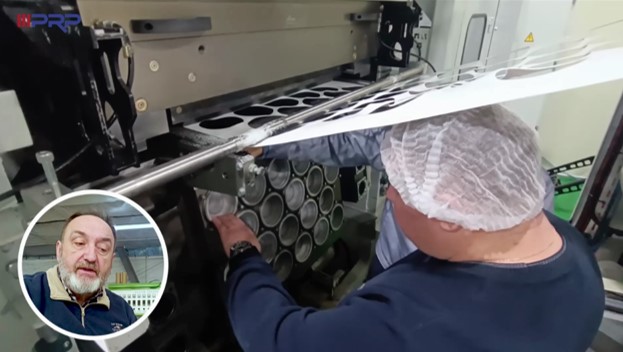
… И в конечном итоге самым интересным оказался узел вырубки, то есть конструкция матриц-пуансонов, выталкивателей, потому что в этом случае важно совмещение инструмента очень точной контурной вырубки. Поэтому конструкция защиты лезвий, размещение лотка и процесс удаления – они очень-очень щепетильны, вплоть до того, насколько точно настраиваются по отношению другу матрица и пуансон. Там наши руки тоже побывали, мы пощупали практически каждый из узлов.
Машину, безусловно, наши партнеры при этом остановили, но вы видите, насколько удобен доступ к оборудованию, даже к крупному. И только после того, как руки побывали внутри машины, клиент получил полные исчерпывающие ответы на свои вопросы, потому что вырубка готового изделия, его товарный вид, гарантия герметичности в данном случае для ретортной упаковки — это один из самых крутых моментов.
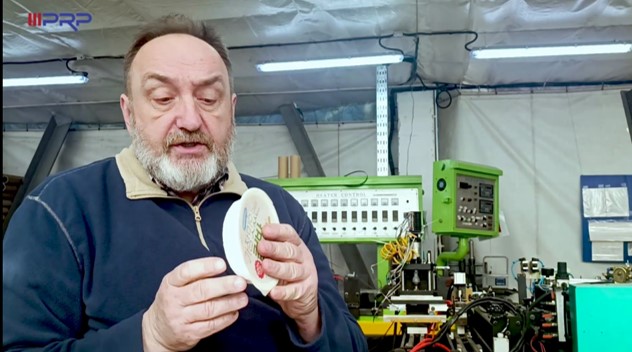
В руках я сейчас держу как раз один из образцов изделия, которое сформовано именно на этом оборудовании, в этот лоток загружается продукт, в данном случае рис. Запаивается верхней покрывной плёнкой, и уже в процессе в автоклаве этот продукт доводится до готовности, чтобы с длительным сроком хранения предложить его на рынок потребителю.
Ну что ж, в этом ролике, ребята, вы увидели, как производится толстая, трёхслойная, а точнее, пятислойная барьерная плёнка с использованием слоя EVOH. Это как раз тот высокобарьерный материал для жестких лотков, который многие хотят использовать для своего продукта. Это — так называемая лоток-тарелка.
Материал не самый дешёвый, но когда вы ратуете за свой продукт, когда вы видите, что продукт получается очень вкусным во время приготовления его методом стерилизации или бережного автоклавирования, то стоимость лотка при этом нивелируется теми удобствами и преимуществами, которые дает нам эта упаковка.
В России подобное производство ещё пока не освоено, но могу сказать, строительство подобного завода идёт, и нам успешно в этом помогают индусы, как ни странно, потому что Европа отказалась от России в настоящий момент. Но вскоре и в России уже будут производить лотки любой конфигурации по требованию заказчика для того, чтобы удобно пользоваться ими, ну и соответственно, чтобы цена изделия была вполне разумной.
Спасибо, ребята, что вам удалось посмотреть и этот ролик.
Возможно, он был не такой интересный как другие, но всё же мы стараемся вам показать, как производятся барьерные материалы. Кто-то будет смотреть, кто-то будет пропускать мимо своих ушей и носа, но, так или иначе, вы всегда сможете что-то узнать. Для тех, кто смотрел первый раз — это здорово, для тех, кто хочет и далее получать информацию, будет здорово, если вы подпишетесь на наш канал.